Alright, so i searched through the thread list to find ANY request/help thread for maya that i could post this in, but couldn't find anything. so as much as i hate making a whole thread for my dumb questions, it's what i gotta do. Basically, i'm using maya to convert .OBJs to .STLs, as well as tweaking stuff in general. one of the tweaks i gotta do is cutting some of the files into pieces so they can fit on the 3D printer's build plate, like so:
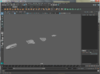
Problem is, when i cut them into pieces, it leaves a hole and makes my slicer throw a big tantrum about the faces. now, the best help i could find from googling and scouring Autodesk's forums was the "fill hole" function, which worked on some smaller, much simpler holes on other models, but when it came to the ship pictured above, it won't close the holes! any ideas on how to help?
Here's the file for anyone that wants to take a look for themselves:
https://www.4shared.com/file/TNKsTRwtba/CAS-Class_Cruiser_seperated.html
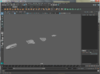
Problem is, when i cut them into pieces, it leaves a hole and makes my slicer throw a big tantrum about the faces. now, the best help i could find from googling and scouring Autodesk's forums was the "fill hole" function, which worked on some smaller, much simpler holes on other models, but when it came to the ship pictured above, it won't close the holes! any ideas on how to help?
Here's the file for anyone that wants to take a look for themselves:
https://www.4shared.com/file/TNKsTRwtba/CAS-Class_Cruiser_seperated.html