glasscutter
Jr Member
Hi 405th! After researching here and building a helmet for my kids Halloween costume, it's time for my full suit. This build will be a Mark VI armor set from Halo 3. The goal is to use Aqua-Resin to replace epoxy/polyester resin and Bondo. This will not be a fast build. I am guessing 10 months to 1 1/2 years. I'm not in any hurry to finish and the usual excuses apply (family/job/part time school/laziness lol).
I couldn't even begin without thanking everyone on here for posting information. All the hard work by 405th members have made this build possible.
During this build if anyone has comments, criticism, or tips/hints to make something better, please don't hesitate to say so. All feedback is good, both negative and positive. Just be forewarned, I like to ask lots of questions lol.
First piece up will be: MKVI_HD_RightHandPlate_ROBOGENESIS
Edit (1/30/2014): Change in plans. The plague has hit home in the form of a nasty cold. Things have definitely slowed a bit. Also I planned to use chip board for the hand plate indents, but its backordered. Second problem is the edge id's overlap the fold lines too much on the HD files so far. Moved to the forearm and turned off edge id. The prospect of assembly without them makes me kind of nervous. Anyway, I have moved to MKVI_HD_FOREARM_RIGHT_NUGGET_LETTER. Parts are cut and folded for assembly hopefully this weekend!
Edit2 (2/16/2014) Another change in plans. Switching from Mk VI to a Halo:CE Mk V build. I feel the need to go old school.
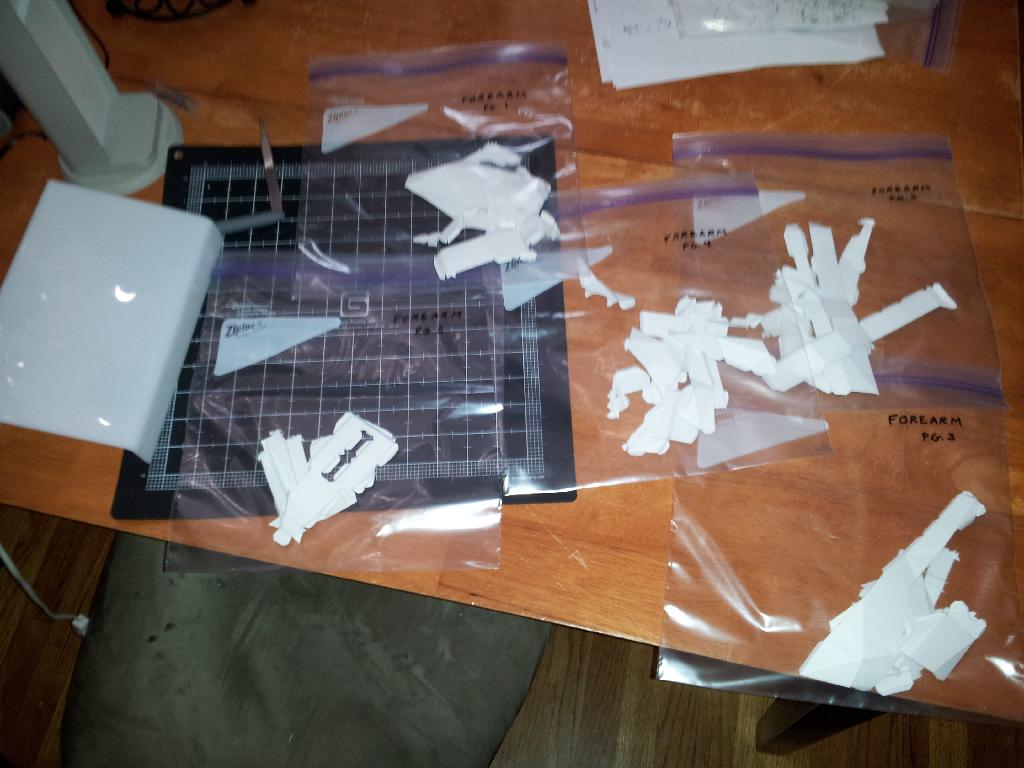
Also managed to get a collapsible paint booth set up.
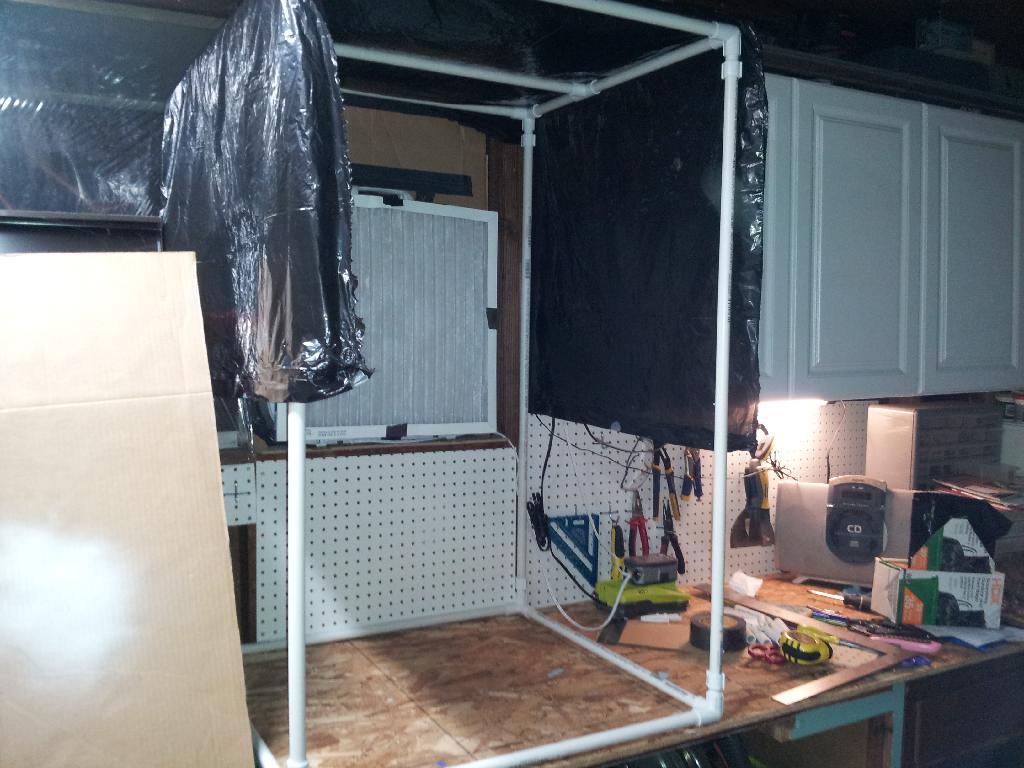
I couldn't even begin without thanking everyone on here for posting information. All the hard work by 405th members have made this build possible.
During this build if anyone has comments, criticism, or tips/hints to make something better, please don't hesitate to say so. All feedback is good, both negative and positive. Just be forewarned, I like to ask lots of questions lol.
First piece up will be: MKVI_HD_RightHandPlate_ROBOGENESIS
Edit (1/30/2014): Change in plans. The plague has hit home in the form of a nasty cold. Things have definitely slowed a bit. Also I planned to use chip board for the hand plate indents, but its backordered. Second problem is the edge id's overlap the fold lines too much on the HD files so far. Moved to the forearm and turned off edge id. The prospect of assembly without them makes me kind of nervous. Anyway, I have moved to MKVI_HD_FOREARM_RIGHT_NUGGET_LETTER. Parts are cut and folded for assembly hopefully this weekend!
Edit2 (2/16/2014) Another change in plans. Switching from Mk VI to a Halo:CE Mk V build. I feel the need to go old school.
Also managed to get a collapsible paint booth set up.