First of all, maybe a little what, why, when, ...
- How I got into this: I got the idea of building a Stormtrooper helmet after I first visited FACTS (one of the few conventions we have here in our little country), saw some guys of the 501st there and really liked the idea of owning such a helmet / suit of my own. I started looking on the Interwebs to buy a suit, but to be completely honest I have to admit the price of a full armour is way to steep for my earnings. Started looking for alternatives and came onto Pepakura, with some googling I ended up on this forum and found tons of inspiration here, so I finally decided to start my adventure to try and make that Helmet. If the helmet would turn out OK'ish I think I'm also gonna try the suit, but that's for later.
- Why the 'Belgian Build' reference in the title: As I was preparing myself to start the project I encountered some bumps along the road, mainly in finding the right materials. We don't have Walmarts or anything of that sort in Belgium, Bondo as a brand is not available on the market here, so I did the research where to find what and how to search for it without using Brand names and I thought: "Why not share this with other Belgians who might be interested in building a helmet / suit". This is also why I'll be listing the stuff I used and where I got it along this thread. I'll also mention the stuff I used which I ditched along the way cause they didn't fit my way of building, I know this is personal, but it might help you avoid some traps along the road.
Do mind I'll mention the stores where I found my stuff (mostly chains found throughout the country), it is still possible you find your stuff in other stores offcourse.
So here we go:
Materials
- Paper: I started out using 200g/m² printing paper as I tought this to be the same as the mentioned 'cardboard', it isn't!
Where did I find cardboard, @ Hema, and cheap too, € 2,5 / kilogram (no mention on the package how many sheets are in it, but it's 1 kg of paper, and certainly enough for a helmet)
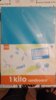
Only disadvantage (maybe) that it's coloured paper, 10 different colours and there's not enough sheets of any given colour to completely print the helmet on same colour paper.
- Glue: I made two helmets (one that was way too small, one that was way too big) using a hot glue gun, though there are advantages to the glue gun (glues fast and rock solid), I found there are disadvantages too (very hard to work clean on detailed portions, glue strings, risk of burning, very short correction time) so I switched to regular all purpose glue (alleslijm) (found @ Action for € 1). I apply this glue with a cotton swab (oorstokje) so it's applied thin and is evenly spread out, it has the right amount of correction time making precise work that much easier.
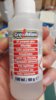
If you would like to try the hot glue gun non the less, you can buy one @ Action for € 3, glue sticks are available there also (€ 1 / 10 sticks). Also available @ Euroshop.
- Cutting Mat / X-Acto knife:
The cutting mat is fairly easy to get, bought this @ Euroshop (€ 9), can also be found @ Ava, Atita, Fun, Dreamland, ...
The X-Acto knife I bought in a store that was specialised in miniature trains, but that doesn't exist anymore. Can be found mostly in hobby stores where the sell miniature cars / warhammer and that sort of things (Verbrugghe Neverland in Bruges & Kortrijk, Albion Kortrijk, Black Border Roeselare, ...)
- Handy things to have:
Metal ruler (I chose a 15cm one, find it easier to handle then a 30cm one), can be found anywhere.
A pair of scissors.
Something to put your helmet on, I made a construction out of Styrofoam and some wooden planks I had lying around.
When I start working on the resin part, I'll post where I got those products as well.
Measuring
I really had trouble with the measuring, which is obvious since I've allready made 2 helmets that didn't fit. Before I started on the third one I received a great tip for measuring your head. Open a door, put your head in between and close the door untill it touches your ear, pull your head back gently, keeping the door @ the exact width of your head and measure the gap. Then add about 3-4 cm (in total). In my case that came to 21cm. With the 'Measure distance between two points' feature in Pepakura I then measured the distance between the most narrow point my head had to fit through and made sure that was also 21cm (in this helmet it's the distance between the 2 indents on the side helmet).
The works
I'll put some pics here of the first 2 (testing, learning pepakura) helmets I made and then the start of my 3rd (and hopefully final) one, I'll then update whenever I made significant progress.
Helmet 1:
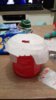
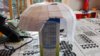
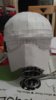
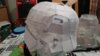
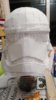
Helmet 2:
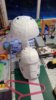
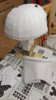
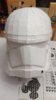
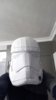
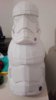
Helmet 3:
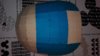
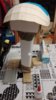
- How I got into this: I got the idea of building a Stormtrooper helmet after I first visited FACTS (one of the few conventions we have here in our little country), saw some guys of the 501st there and really liked the idea of owning such a helmet / suit of my own. I started looking on the Interwebs to buy a suit, but to be completely honest I have to admit the price of a full armour is way to steep for my earnings. Started looking for alternatives and came onto Pepakura, with some googling I ended up on this forum and found tons of inspiration here, so I finally decided to start my adventure to try and make that Helmet. If the helmet would turn out OK'ish I think I'm also gonna try the suit, but that's for later.
- Why the 'Belgian Build' reference in the title: As I was preparing myself to start the project I encountered some bumps along the road, mainly in finding the right materials. We don't have Walmarts or anything of that sort in Belgium, Bondo as a brand is not available on the market here, so I did the research where to find what and how to search for it without using Brand names and I thought: "Why not share this with other Belgians who might be interested in building a helmet / suit". This is also why I'll be listing the stuff I used and where I got it along this thread. I'll also mention the stuff I used which I ditched along the way cause they didn't fit my way of building, I know this is personal, but it might help you avoid some traps along the road.
Do mind I'll mention the stores where I found my stuff (mostly chains found throughout the country), it is still possible you find your stuff in other stores offcourse.
So here we go:
Materials
- Paper: I started out using 200g/m² printing paper as I tought this to be the same as the mentioned 'cardboard', it isn't!
Where did I find cardboard, @ Hema, and cheap too, € 2,5 / kilogram (no mention on the package how many sheets are in it, but it's 1 kg of paper, and certainly enough for a helmet)
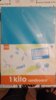
Only disadvantage (maybe) that it's coloured paper, 10 different colours and there's not enough sheets of any given colour to completely print the helmet on same colour paper.
- Glue: I made two helmets (one that was way too small, one that was way too big) using a hot glue gun, though there are advantages to the glue gun (glues fast and rock solid), I found there are disadvantages too (very hard to work clean on detailed portions, glue strings, risk of burning, very short correction time) so I switched to regular all purpose glue (alleslijm) (found @ Action for € 1). I apply this glue with a cotton swab (oorstokje) so it's applied thin and is evenly spread out, it has the right amount of correction time making precise work that much easier.
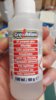
If you would like to try the hot glue gun non the less, you can buy one @ Action for € 3, glue sticks are available there also (€ 1 / 10 sticks). Also available @ Euroshop.
- Cutting Mat / X-Acto knife:
The cutting mat is fairly easy to get, bought this @ Euroshop (€ 9), can also be found @ Ava, Atita, Fun, Dreamland, ...
The X-Acto knife I bought in a store that was specialised in miniature trains, but that doesn't exist anymore. Can be found mostly in hobby stores where the sell miniature cars / warhammer and that sort of things (Verbrugghe Neverland in Bruges & Kortrijk, Albion Kortrijk, Black Border Roeselare, ...)
- Handy things to have:
Metal ruler (I chose a 15cm one, find it easier to handle then a 30cm one), can be found anywhere.
A pair of scissors.
Something to put your helmet on, I made a construction out of Styrofoam and some wooden planks I had lying around.
When I start working on the resin part, I'll post where I got those products as well.
Measuring
I really had trouble with the measuring, which is obvious since I've allready made 2 helmets that didn't fit. Before I started on the third one I received a great tip for measuring your head. Open a door, put your head in between and close the door untill it touches your ear, pull your head back gently, keeping the door @ the exact width of your head and measure the gap. Then add about 3-4 cm (in total). In my case that came to 21cm. With the 'Measure distance between two points' feature in Pepakura I then measured the distance between the most narrow point my head had to fit through and made sure that was also 21cm (in this helmet it's the distance between the 2 indents on the side helmet).
The works
I'll put some pics here of the first 2 (testing, learning pepakura) helmets I made and then the start of my 3rd (and hopefully final) one, I'll then update whenever I made significant progress.
Helmet 1:
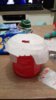
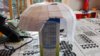
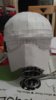
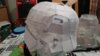
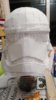
Helmet 2:
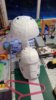
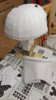
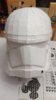
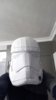
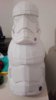
Helmet 3:
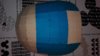
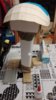
Last edited by a moderator: