Hey guys, I'm back from college and I decided to try tackle a custom Destiny Warlock Helmet. I've got the thing pepakura'd already. It is quite tight to put on, but I can just cut away and make the neck opening bigger later. For my other helmet builds with Pepakura, I have tried to strengthen it using fiberglass and resin once, and the other time I used Rondo on the inside and just resin on the outside; both times failed to achieve what I wanted. I'm leaning towards just doing fiberglass and resin again for this helmet and hopefully doing it better this time but I'm open to any suggestions as to how to strengthen the thing and keep the details nice. Will keep you guys posted on the build.
- Togo
P.S. Here's the link for the Warlock build thread by fellow member Ghost Bear 027 http://www.405th.com/showthread.php/41579-Destiny-Warlock-Helmet-and-Pepakura-file
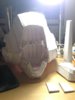
- Togo
P.S. Here's the link for the Warlock build thread by fellow member Ghost Bear 027 http://www.405th.com/showthread.php/41579-Destiny-Warlock-Helmet-and-Pepakura-file
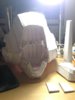