- Member DIN
- S128
I got a little surprise during Turbo's last visit to the States... It's a 3d-Printed Halo Reach Target Locator!!!
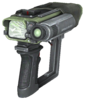
We don't have many "finishing-a-3d-print-walkthroughs" so I thought I'd post my progress on this one. The goal is for Vancouver Fan Expo Feb 15th. (One Month)
First step is to clean up the print. (the real first step is determining if your print is PLA or ABS. Mine is PLA. If yours is ABS then my techniques may not work for you.)
Take a craft knife and start knocking off all the support pieces to make as clean of edges as you can.
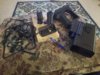
You may need to sand (or file) some of those edges due to imperfections, heavy saturation lines, or just to make them flat. I also sanded down the fake screws so I can add real screws later.
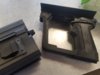
Sanding plastic creates pretty crazy burrs. You can grab your craft knife again to cut them away. I recently picked up a Metal Deburring Tool and think it makes pretty quick work of it.
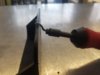
UP NEXT
Before gluing I'm going to see if I can plan out any electronics I might want to add to this guy.
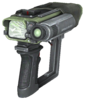
We don't have many "finishing-a-3d-print-walkthroughs" so I thought I'd post my progress on this one. The goal is for Vancouver Fan Expo Feb 15th. (One Month)
First step is to clean up the print. (the real first step is determining if your print is PLA or ABS. Mine is PLA. If yours is ABS then my techniques may not work for you.)
Take a craft knife and start knocking off all the support pieces to make as clean of edges as you can.
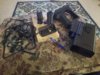
You may need to sand (or file) some of those edges due to imperfections, heavy saturation lines, or just to make them flat. I also sanded down the fake screws so I can add real screws later.
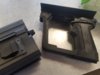
Sanding plastic creates pretty crazy burrs. You can grab your craft knife again to cut them away. I recently picked up a Metal Deburring Tool and think it makes pretty quick work of it.
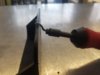
UP NEXT
Before gluing I'm going to see if I can plan out any electronics I might want to add to this guy.
Last edited: