Hey Everyone,
Things took a bit more time then I thought, mind you, most of it was a learning experience and to properly cure Aqua Resin you really need to wait 24 to 48 hours before sanding and applying the next layer. It also took awhile before I improved my technique so I think I've redone a few layers I had just sanding pretty much back again.
I've all ready glued together the first thigh and I place to build a few more things before I start resinning again so I can get a bit of momentum going.
That all said, I have two questions before continuing:
1) can anyone suggest a good pepakura file for a Reach boot, something I can build around a normal shoe.
2) At the end there is a picture of my daughter putting the pieces on just to check size and see if I'm on the right track. I plan to pad the inside with foam for softness but putting the shin on is already a tight fit. I've seen some people cut the back out but I'm a bit hesitant to do so. Does anyone have suggestions, what works best here?
So this is after one extra layer of Aqua Resin and sanding it, still a very rough result (most pictures were taken late at night so sorry for the bad lighting):

This is after putting on the second layer and sanding it back:
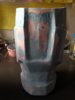
Note that I only just put the top thingy on (and yes I did the sides wrong, check your reference material!!
I'll be making the same mistake on purpose once I do the other side) so that is very rough.
I also put a small video on youtube:
And here is where we got to this morning:
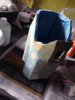
Ignore for a moment the pieces aren't positioned properly, I am a little worried the thigh is ending up too high, we'll see once we finish the COD (which I'm tempted to redo because it suffered a similar but less bad fate as my helmet).
The thigh piece I'm going to see if I can get perfect the techniques I'm using and am planning to describe the other side in a bit more detail. I might put some more vids online as I try out some things and maybe get some feedback on how I'm approaching a few things.
Things took a bit more time then I thought, mind you, most of it was a learning experience and to properly cure Aqua Resin you really need to wait 24 to 48 hours before sanding and applying the next layer. It also took awhile before I improved my technique so I think I've redone a few layers I had just sanding pretty much back again.
I've all ready glued together the first thigh and I place to build a few more things before I start resinning again so I can get a bit of momentum going.
That all said, I have two questions before continuing:
1) can anyone suggest a good pepakura file for a Reach boot, something I can build around a normal shoe.
2) At the end there is a picture of my daughter putting the pieces on just to check size and see if I'm on the right track. I plan to pad the inside with foam for softness but putting the shin on is already a tight fit. I've seen some people cut the back out but I'm a bit hesitant to do so. Does anyone have suggestions, what works best here?
So this is after one extra layer of Aqua Resin and sanding it, still a very rough result (most pictures were taken late at night so sorry for the bad lighting):
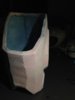

This is after putting on the second layer and sanding it back:
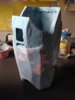
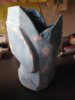
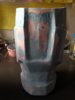
Note that I only just put the top thingy on (and yes I did the sides wrong, check your reference material!!
I also put a small video on youtube:
And here is where we got to this morning:
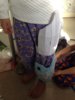
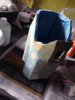
Ignore for a moment the pieces aren't positioned properly, I am a little worried the thigh is ending up too high, we'll see once we finish the COD (which I'm tempted to redo because it suffered a similar but less bad fate as my helmet).
The thigh piece I'm going to see if I can get perfect the techniques I'm using and am planning to describe the other side in a bit more detail. I might put some more vids online as I try out some things and maybe get some feedback on how I'm approaching a few things.
Last edited by a moderator: