Thanks starvinartist80, I brought you guys photos to explain how I do things!
Here is one of the problem area's. I chopped this open with a knife.
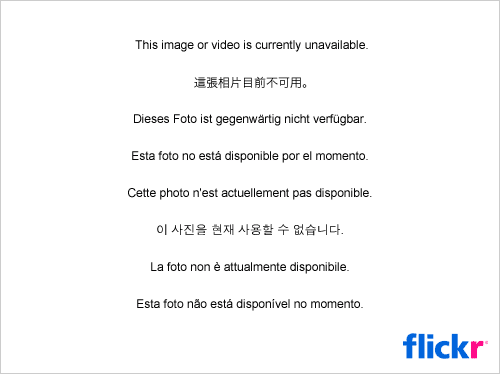
Here is the front bill that also has a void that i've removed the paper. This one was HUGE so I was afraid as I cut away.
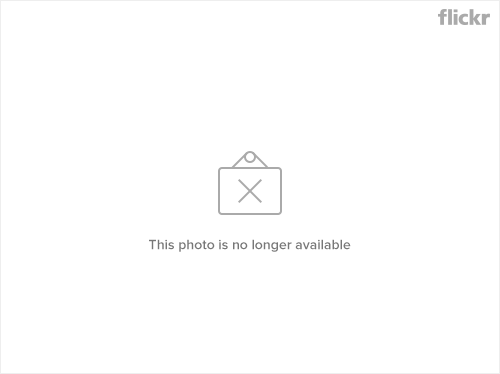
I have now back filled the area. I used some really hot rondo so that it would stay in place and help fix the fact that the fibreglass didn't get resin on it.
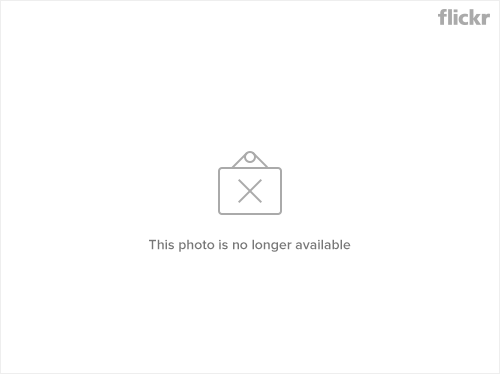
Here is how it looks on the front of the bill as well

Tomorrow I will be putting some normal bondo on top and start to sand it down.
Here is one of the problem area's. I chopped this open with a knife.
Here is the front bill that also has a void that i've removed the paper. This one was HUGE so I was afraid as I cut away.
I have now back filled the area. I used some really hot rondo so that it would stay in place and help fix the fact that the fibreglass didn't get resin on it.
Here is how it looks on the front of the bill as well
Tomorrow I will be putting some normal bondo on top and start to sand it down.