- Member DIN
- S068
I get a lot of requests to help build helmets and because of it I wanted to develop a relatively quick and painless approach to making one-off visors that look good and don't break the bank. If everything just used a standard motorcycle visor that'd be awesome but we're not so lucky in the world of Halo where things like the Warmaster helmet exist.
For this tutorial [?] I'm going to be using a recent commission build as an example for visor construction because I document projects a lot better when I'm making them for someone that's not me. The helmet used is Bondrewd's helmet from Made in Abyss.
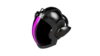
It's a long sloping form with complex curves and requires a tight fit into the surrounding shell to properly obscure the wearers face so fit tolerances are tight and we can't get away with a pre-made solution. Enter the super cheap vac former setup! The materials used in this all came out to less than $50CAD including a 30"x40" sheet of 1/32" PETG. You may require more or less materials than I did overall based on the size of your heating element, I was restricted to 9.5"x8" which is the interior size of the toaster oven that I procured.
Materials
The top of the box is a simple rectangle of pegboard or hardboard with a grid of holes drilled through to allow air to be pulled through the box and into the vacuum. The bottom of the box is a rectangle the same size as your top but using the cheapest sturdy material available, I used hardboard. The four side walls are then built up using a slightly thicker material (1/4" MDF) cut to length to surround the box and have a height 1/4" larger than the diameter of your vacuum hose to allow for attachment to the box while minimizing air gap in the box which will keep everything working efficiently.
When assembling the box, hearty application of wood glue is necessary to make sure the fit is air tight. If you do have air leaks outside of the top grid, these can be plugged later with the handyman's secret weapon or a similar flexible gap covering tool. I use a combination of wood glue and nails to keep the top surface connected and ground any nail heads that were proud of the surface down flush.
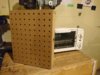
For the frame that will hold the plastic inside the toaster oven I used hardboard cut into thin 1/4" bounding frames that are held together using binder clips. Using two frames and a sheet of PETG you want to make a plastic sandwich that you will clip in place. When heating up the plastic will deform and the clips prevent it from slipping free of the frame and falling onto the hot element.
Because you're working with plastics and hot things at the same time, the concept of off-gassing comes into play here. You want a paint and pesticide rated respirator as well as ventilation when doing this. When heating up PETG it makes very unfriendly fumes. Heat resistant gloves are also a nice to have too if you don't have the cold, dead and scarred hands of a cosplayer.
Yes wood burns but doing your homework lets you save money and use leftovers from building your former box. The ignition temperature of MDF is over 400°F and the magic number on most PETGs for forming is between 280°F and 320°F. That being said, hot things are hot and keep a fire extinguisher (ABC Dry Chem is always a good choice) nearby when working with things like this. With a visor buck ready to go, cut the PETG sheeting to the size of your frame and start heating up the toaster oven to your desired temperature. Most suppliers will have a data sheet with temperature ranges for working with their product but if not you can always look up the Technical Data Sheet of the plastic and look for the "Glass Transition Temperature" to get a good range to start working with.
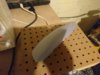
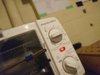
Always have more sheeting than you need if you've never worked with a specific plastic before because you will bork it at least once or twice. You want the plastic to become malleable gradually and evenly so a slow approach to the transition temperature is usually a good practice. Set your heat below that temperature to let the plastic warm evenly and then set it to the known temperature and let the plastic begin to bow and droop down. Once your plastic is near the heating element like in my case, quickly remove the frame and plastic from the heat, turn on the vacuum and press the frame over the buck to get a nice copy of your visor shape. If there's some points that don't have all the details fully captured you can use a heatgun and careful stretching of the plastic to fix any defects but it will introduce more of a beer-goggles effect from uneven thicknesses of material that you're looking through. It's usually best to retry and get another pull.
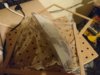
Did I mention poison? Yes! This procedure uses a bunch of wicked awesome chemicals and composites that can kill you dead so we're basically just using old hand me down and thrift store find kitchen equipment that will never see use on food ever again. Say it one more time with me so everyone in the back can hear and remember. WE NEVER USE THIS KITCHEN EQUIPMENT FOR FOOD EVER AGAIN.
Dyeing Materials
First off the dye needs to be dissolved into boiling water and then have a colour intensifier added. There will be a bit of smell with this stuff so having the range fan and an open window is advised. Also it's dye so don't get it on yourself or your clothes. Before you add your thermoplastic into the hot dye, let the pot of dye cool to at least 145°F or you'll have to go reform your visor.
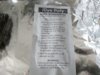
Trim down the visor and leave a bit of flashing on the edges so that you can drill a hole that you can hook a paperclip through. Then hook the paperclip over a bent wire hanger so that you can dip your visor into the dye. Leave the visor in the dye for several minutes and then quench it in cold/ice water to lock the colour in. If you want a more vibrant colour, let it sit in the dye for several minutes and repeat the quenching cycle until you have your desired colour.
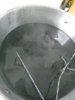
Once you have the colour you like, rinse it thoroughly in cold water to remove any residue or remaining dye on the surface.
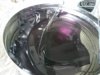
Then all that's left is to go install your super cool new coloured visor and impress all the other boys and girls with your handiwork.
If I was unclear on any of the steps, feel free to give a shout and I can edit my original post or answer you directly in the comments!
For this tutorial [?] I'm going to be using a recent commission build as an example for visor construction because I document projects a lot better when I'm making them for someone that's not me. The helmet used is Bondrewd's helmet from Made in Abyss.
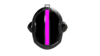
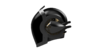
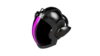
It's a long sloping form with complex curves and requires a tight fit into the surrounding shell to properly obscure the wearers face so fit tolerances are tight and we can't get away with a pre-made solution. Enter the super cheap vac former setup! The materials used in this all came out to less than $50CAD including a 30"x40" sheet of 1/32" PETG. You may require more or less materials than I did overall based on the size of your heating element, I was restricted to 9.5"x8" which is the interior size of the toaster oven that I procured.
Materials
- Toaster Oven or similar heat source that will never heat food again
- 1/4" MDF or similar
- 1/8" Pegboard (easiest option, I'd suggest using hardboard and hand drilling smaller gauge holes)
- 1/8" Hardboard
- Woodglue
- Shop Vac or other vacuum cleaner
- 1/32" PETG or Lexan
- Binder clips or similar low profile clamps
The top of the box is a simple rectangle of pegboard or hardboard with a grid of holes drilled through to allow air to be pulled through the box and into the vacuum. The bottom of the box is a rectangle the same size as your top but using the cheapest sturdy material available, I used hardboard. The four side walls are then built up using a slightly thicker material (1/4" MDF) cut to length to surround the box and have a height 1/4" larger than the diameter of your vacuum hose to allow for attachment to the box while minimizing air gap in the box which will keep everything working efficiently.
When assembling the box, hearty application of wood glue is necessary to make sure the fit is air tight. If you do have air leaks outside of the top grid, these can be plugged later with the handyman's secret weapon or a similar flexible gap covering tool. I use a combination of wood glue and nails to keep the top surface connected and ground any nail heads that were proud of the surface down flush.
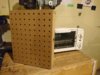
For the frame that will hold the plastic inside the toaster oven I used hardboard cut into thin 1/4" bounding frames that are held together using binder clips. Using two frames and a sheet of PETG you want to make a plastic sandwich that you will clip in place. When heating up the plastic will deform and the clips prevent it from slipping free of the frame and falling onto the hot element.
Because you're working with plastics and hot things at the same time, the concept of off-gassing comes into play here. You want a paint and pesticide rated respirator as well as ventilation when doing this. When heating up PETG it makes very unfriendly fumes. Heat resistant gloves are also a nice to have too if you don't have the cold, dead and scarred hands of a cosplayer.
Yes wood burns but doing your homework lets you save money and use leftovers from building your former box. The ignition temperature of MDF is over 400°F and the magic number on most PETGs for forming is between 280°F and 320°F. That being said, hot things are hot and keep a fire extinguisher (ABC Dry Chem is always a good choice) nearby when working with things like this. With a visor buck ready to go, cut the PETG sheeting to the size of your frame and start heating up the toaster oven to your desired temperature. Most suppliers will have a data sheet with temperature ranges for working with their product but if not you can always look up the Technical Data Sheet of the plastic and look for the "Glass Transition Temperature" to get a good range to start working with.
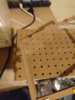
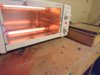
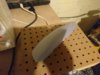
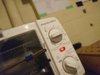
Always have more sheeting than you need if you've never worked with a specific plastic before because you will bork it at least once or twice. You want the plastic to become malleable gradually and evenly so a slow approach to the transition temperature is usually a good practice. Set your heat below that temperature to let the plastic warm evenly and then set it to the known temperature and let the plastic begin to bow and droop down. Once your plastic is near the heating element like in my case, quickly remove the frame and plastic from the heat, turn on the vacuum and press the frame over the buck to get a nice copy of your visor shape. If there's some points that don't have all the details fully captured you can use a heatgun and careful stretching of the plastic to fix any defects but it will introduce more of a beer-goggles effect from uneven thicknesses of material that you're looking through. It's usually best to retry and get another pull.
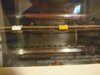
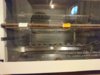
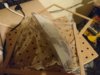
Did I mention poison? Yes! This procedure uses a bunch of wicked awesome chemicals and composites that can kill you dead so we're basically just using old hand me down and thrift store find kitchen equipment that will never see use on food ever again. Say it one more time with me so everyone in the back can hear and remember. WE NEVER USE THIS KITCHEN EQUIPMENT FOR FOOD EVER AGAIN.
Dyeing Materials
- Big ol' metal cooking pot
- Equally big ol' container
- A thermometer
- Metal coat hanger or similar wire
- Paperclips
- Jacquard iDye Poly
First off the dye needs to be dissolved into boiling water and then have a colour intensifier added. There will be a bit of smell with this stuff so having the range fan and an open window is advised. Also it's dye so don't get it on yourself or your clothes. Before you add your thermoplastic into the hot dye, let the pot of dye cool to at least 145°F or you'll have to go reform your visor.
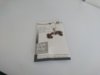
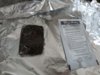
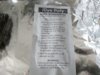
Trim down the visor and leave a bit of flashing on the edges so that you can drill a hole that you can hook a paperclip through. Then hook the paperclip over a bent wire hanger so that you can dip your visor into the dye. Leave the visor in the dye for several minutes and then quench it in cold/ice water to lock the colour in. If you want a more vibrant colour, let it sit in the dye for several minutes and repeat the quenching cycle until you have your desired colour.
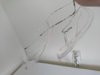
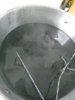
Once you have the colour you like, rinse it thoroughly in cold water to remove any residue or remaining dye on the surface.
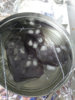
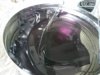
Then all that's left is to go install your super cool new coloured visor and impress all the other boys and girls with your handiwork.
If I was unclear on any of the steps, feel free to give a shout and I can edit my original post or answer you directly in the comments!