Rayg3Qwitt
New Member
I started this build yesterday and have made some good progress. Don't worry about the pink, my wife is a teacher and only had pink cardstock lol. I found it fairly easy to cut, glue and resin the helmet. My plan was to build the helmet first (hardest part) and if I can do that, then the rest should be doable.
I just fiber glassed the inside of the helmet. I used Fiberglass Resin and Fiberglass mat. Hindsight being 20/20 I would have liked to use the cloth. It looked less stringy. In the end I only had a small handful of strings poking up that were easily snipped with scissors. The helmet feels solid (except for around the neck where I couldn't quite get the fiberglass mat to cooperate. It is covered in resin though.
From the moment I downloaded the pep software I have about 12 hours of solid work into this helmet already. Quite the project, but I am super stoked about it.
It begins...
I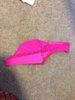
Gluing is done. I am happy with my very first pep glue job.
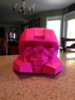
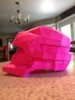
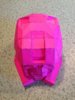
Got the fiberglass done and outer coat of resin. It feels strong. I'm not to concerned in making it over reinforced as it will just be used as a costume piece. In the pics (below) the helmet was dry, but it is still curing. Will let it sit over night and see if I need to go over any piece again.
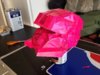
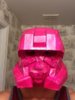
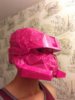
The next step for this helmet is to get some bondo and smooth it out.
My questions at this point:
1. Is it okay if the neckline is not glass reinforced and just resin'd?
2. If this is fully covered in resin is it now waterproof?
3. Do I need to sand the resin before adding bondo?
4. Should I use bondo to add details like vent lines, texture raises etc... Or can I use foam in conjunction with Pep? and just bondo/paint over the foam?
Thank you so much for all the amazing posts. I have been all over the faqs and newcomers posts.
I just fiber glassed the inside of the helmet. I used Fiberglass Resin and Fiberglass mat. Hindsight being 20/20 I would have liked to use the cloth. It looked less stringy. In the end I only had a small handful of strings poking up that were easily snipped with scissors. The helmet feels solid (except for around the neck where I couldn't quite get the fiberglass mat to cooperate. It is covered in resin though.
From the moment I downloaded the pep software I have about 12 hours of solid work into this helmet already. Quite the project, but I am super stoked about it.
It begins...
I
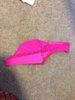
Gluing is done. I am happy with my very first pep glue job.
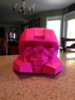
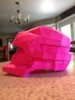
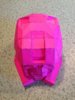
Got the fiberglass done and outer coat of resin. It feels strong. I'm not to concerned in making it over reinforced as it will just be used as a costume piece. In the pics (below) the helmet was dry, but it is still curing. Will let it sit over night and see if I need to go over any piece again.
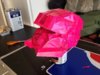
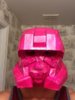
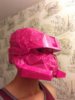
The next step for this helmet is to get some bondo and smooth it out.
My questions at this point:
1. Is it okay if the neckline is not glass reinforced and just resin'd?
2. If this is fully covered in resin is it now waterproof?
3. Do I need to sand the resin before adding bondo?
4. Should I use bondo to add details like vent lines, texture raises etc... Or can I use foam in conjunction with Pep? and just bondo/paint over the foam?
Thank you so much for all the amazing posts. I have been all over the faqs and newcomers posts.