Cosplay4UsAll
New Member
This project had a lot of "firsts" for us. First time making a gun, first time using mdf for a prop, and our first time making a two part mold (we actually made TWO 2 part molds, one for each half of the gun!) to name just a few! It was great fun and a wonderful learning experience (which we love!).
We decided on making the plasma pistol as it had several things we were looking for in our next project. It would involve a two part mold, as we wanted to make the acrylics light up with LEDs, and it was small enough for Courtney to carry, at conventions, for long periods of time. As usual, we got a TON of references to work from. This was one of our primary go-to images.
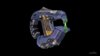
Once we decided the materials we were going to use, a mock up was made and sizing was checked.
Always wear your safety gear (respirator and safety glasses) when working with manufactured "wood" type products.
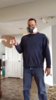
Once we had it sized, the two halves were cut (using a band saw) from 1/2" mdf. Much sanding ensued! At this point, we used tracing paper to copy aaaalll the various layers and details that would be added later in the build process. These were then marked on the mdf halves so we would have an approximation of where things, like screws to keep the gun together, would need to be.
Holes were then drilled (using the drill press) and recessed, in the approximate location of where the "bolts" are in the images. Brass inserts were....inserted.....in to the mdf and, with a couple of allen head screws, would help hold the two halves together. In order to insure an easy way to line the two halves up every time, more holes were drilled from the outside of one half the gun, partially through the inside of the second half. Tiny dowel rods were then shoved through the holes and glued in place.
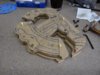
Once the glue set on the dowel rods, they were cut flush to the outside of the gun, and left longer on the inside of that half. They were then sanded smooth on the outside, and cut short enough on the inside to fit snug in to the matching holes inside the second half. This would ensure the two parts would always line up perfectly, and hold together easily, while the two halves are screwed in place.
Here we have our first test fitting. Perfect!!
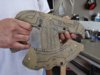
Now that we know the two halves will go together, and STAY together neatly, it is time to make room for the electronics! Lines are drawn on the inside of the two halves, indicating where we need to remove excess material.
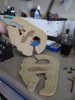
Very carefully, the drill press is used to remove the excess mdf from the insides of the gun. A slow, nerve wracking process indeed, as mdf can chip or crack if manhandled. We were basically cutting the 1/2" mdf down to maybe 1/4" (or less) in the hollowed area.
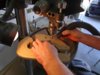
Success! Two halves, minus their "guts".
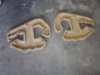
Using some extra blue acrylic we had lying around (there is no such thing as "garbage" to a prop maker, lol), we mocked up and test fit the acrylic tips. These would eventually be made from edge lit neon green acrylic. The trigger (currently made from a thick piece of scrap pvc foam board) is cut and test fit in place as well.
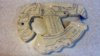
Once we knew how much room we had, teeny tiny switches were ordered (you won't find these in your local RadioShack!). Awww aren't they cute! Simple, spring loaded switch that will push the "trigger" back out, once you release it.
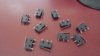
The mdf is sealed with several coats of wood glue (a sticky project, for sure!) to help smooth its rough texture. Lots of sanding, followed by a couple of coats of primer, and more sanding.
Detail pieces are added using a variety of materials in various thicknesses. Some of them were so rounded we decided to use different types of craft foam, since it would wrap around things so easily.
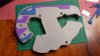
Different thicknesses of pvc foam board (aka Sintra) were also used to add the rest of the layers of details.
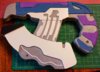
Since we were now sure exactly where the acrylic, trigger and electronics were all going to sit inside the gun, Apoxy Sculpt was used in several areas to help keep things in place, once it was all assembled.
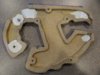
All the details have been added, craft foam was sealed with Mod Podge, and some light sanding was done on the Sintra edges. Then the whole thing got a couple of coats of primer and sanded smooth.
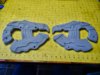
Since we obviously wanted to be able to take the two halves apart (for battery replacement, etc), we would have to make TWO 2 part molds!
Mold boxes were made with some extra foam core board we had laying around (again....no such thing as "garbage", lol). Then it was on to carefully claying them in place (sulfur free clay!) and add the registration keys. These are important as they will ultimately be used to put the two halves back together again, keeping them lined up perfectly. These were made with the end of a Sharpie.
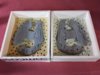
The first attempt we made at molding this was made very late at night (mistake #1) and was our first time using a new scale (mistake #2) and a product we had never tried before (mistake #3).
This is a picture of the CORRECTED mold. The first one we did we had the measuring off, and mixed it 100:1 instead of 10:1. This resulted in a box full of pink goo. Thankfully, the wonderful techs at Smooth-On's helpline helped us save the prop that was submerged under the mess of never-curing silicone. After pouring out the box of goo, we were able to rescue the prop and clean it with Isopropyl alcohol, making sure to get every nook and cranny clean!
A waste of time and money, BUT a very valuable lesson learned!
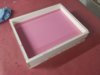
Once we got it right, working with Smooth-On's Mold MAX 30 was a fantastic experience! Our first attempt making any kind of box mold and we got two perfect, bubble free molds!!
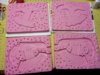
We then cast both halves, using Smooth-On's Smooth Cast 300. Thanks to the molding tips we got from our friends at Punished Props, Volpin Props and WM Armory we were able to get a beautiful, bubble free cast, with minimal seam lines, the very first time! Good thing too, as Dragon Con was fast approaching!
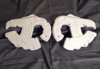
After some very minimal sanding, the brass inserts are in place and the gun is snugged together with allen head screws. Without electronics it weighs around 2.1 pounds. A comfortable balance that gives it a realistic feel, yet won't kill your arm carrying it around all day.
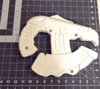
With only a few days left before Dragon Con we were under a time crunch to get this done. The gun was primed and sprayed painted gray. Unfortunately we had very humid weather during this time (figures!) and had several issues with paint bubbling, and refusing to cure. So we sanded where we could and used black and yellow acrylics for the detail areas.
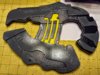
Finding this particular gem at our local Hobbytown was lucky! We have an airbrush gun but have only used it for either spraying body makeup (for our Silent Hill nurse) or latex paint (which clogged the hell out of it!). Finally getting the chance to use it, with actual airbrush paint, was so awesome we plan on using it a lot more in the future. Plus, using the airbrush allowed us to avoid the whole "it is hot and humid as hell and there's no way your rattle can paint will cure in time" issue!
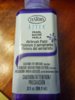
The non-purple areas are taped up and the rest is airbrushed with purple paint with a pearl finish. I really enjoyed this part!
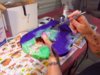
The purple paint is dried and the gun is unwrapped! Eeeeee!
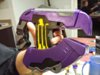
Lots of little details are painted on. Almost done!
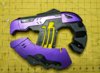
Inside of the gun. The green acrylic tips have had a small hole drilled in them and a small superbright LED inserted in each. These are then wired to the little tiny switch and powered by 3 AAA batteries. The trigger fits perfectly into the grip of the gun.
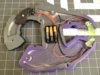
..........................
Last edited by a moderator: