JeffZugale
New Member
I actually got two whole hours to work last night! Amazing.
As planned, I started by gluing the angled side-plate box for the overbarrel onto the barrel block. At first I tried a couple of ways of taping it down to the scrap MDF piece, but that didn't work. I decided to make a jig by sticking some more scrap MDF blocks on with CA glue. That held the angle box in place. Then I slid the barrel block in from the front. Again I tried tape to hold it in place but still not satisfactory. Happily I noticed my 1-2-3 blocks; one of them is plenty heavy enough to hold the block steady. I then squeezed some Titebond 2 down into the gaps, spread it a bit with a toothpick, let gravity pull it in, and set it aside to dry.
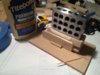
Meanwhile, I turned to the frame and side rails. Clamped them together dry to see how it worked; with this set of frame and rails it's almost exactly the right width, so the rails don't need thickness sanded down. What luck! Got out my ruler and the plans and marked up that assembly for the various cuts, carves and sanding they'll need.
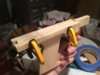
Time to rout out the underbarrel. Found center, marked the width, set the depth and stop line on the routing table... and realized that since I'd shaped the sides already, I wouldn't be able to rout along the straight lines parallel to centerline, oops. Solution: tape a piece of wood on the side that will hold it parallel. I also used a piece of MDF on the fence (not shown) so I could smoothly skip the big shaper gap.
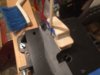
Results: MUCH better than last time. A bit of planning and thinking ahead pays off! And while I did all that, the barrel block dried nicely.
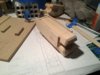
Held together with clamps and hand, by golly it's really starting to look like the thing it's supposed to be!
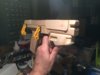
Next week: rout out bits on top block and more on underbarrel, glue top block onto barrel block, carve the side rails. Maybe get some work on the back part of the barrel block where it tapers inward.
As planned, I started by gluing the angled side-plate box for the overbarrel onto the barrel block. At first I tried a couple of ways of taping it down to the scrap MDF piece, but that didn't work. I decided to make a jig by sticking some more scrap MDF blocks on with CA glue. That held the angle box in place. Then I slid the barrel block in from the front. Again I tried tape to hold it in place but still not satisfactory. Happily I noticed my 1-2-3 blocks; one of them is plenty heavy enough to hold the block steady. I then squeezed some Titebond 2 down into the gaps, spread it a bit with a toothpick, let gravity pull it in, and set it aside to dry.
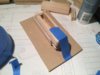
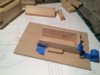
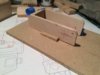
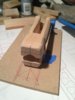
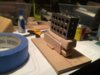
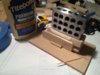
Meanwhile, I turned to the frame and side rails. Clamped them together dry to see how it worked; with this set of frame and rails it's almost exactly the right width, so the rails don't need thickness sanded down. What luck! Got out my ruler and the plans and marked up that assembly for the various cuts, carves and sanding they'll need.
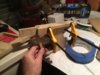
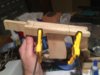
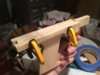
Time to rout out the underbarrel. Found center, marked the width, set the depth and stop line on the routing table... and realized that since I'd shaped the sides already, I wouldn't be able to rout along the straight lines parallel to centerline, oops. Solution: tape a piece of wood on the side that will hold it parallel. I also used a piece of MDF on the fence (not shown) so I could smoothly skip the big shaper gap.
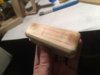
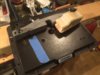
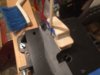
Results: MUCH better than last time. A bit of planning and thinking ahead pays off! And while I did all that, the barrel block dried nicely.
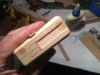
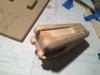
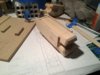
Held together with clamps and hand, by golly it's really starting to look like the thing it's supposed to be!
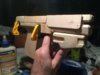
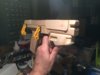
Next week: rout out bits on top block and more on underbarrel, glue top block onto barrel block, carve the side rails. Maybe get some work on the back part of the barrel block where it tapers inward.