- Member DIN
- S2424
Another quick update before the weekend:
Almost finished w/ the foaming of the front of my chest piece. I have some pieces that still need fabrication and some that need modification. As I said, some of the templates are not translating to foam well or even the correct size(!?!?!) Not sure how that happened but This is what I have so far:
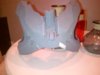
I know......I know.......the center piece is tilting a little to the left, I just couldn't get it to sit straight while holding it till the glue dried. I mighty have to cut out that whole center section and redo. Either the templates were not cut exactly or the foam pieces......or it's just me........I'm also seeing the difference between the pep print-out and the "screen shot".
Pep looks nothing like this
but I'm going to try my best to get it there. Even If I have to lay on a thin layer of foam on top of my armor to get that layered look to the armor. Might get a bit heavy....but it will look better for it. Size-wise, it fits nicely. I started cutting out some of the shoulder pieces for the inside portion, this way it will sit across all of my shoulder rather than 1/2 inch if it. Then its on to the booster pack for the back.....wish I had my mannequin w/ me but I have no room for it at the moment. It would help me knowing if the pieces are pulling too tight as the mannequin is my exact size.....across the chest that is.......he's go the 6 pack and I'm still sporting the keg look........This weekend is going to be nice....so back to the helmet.....got to finish resining and fiber-glassing it up. It was just to rainy out the past few weekends to do w/o potential warping due to moisture.
That's all for now folks, see you after the weekend. Now is time for some fun and sun at the beach.......don't forget the drinks!!!!!! (and I wonder why I still have the spare tire!!!!)
Almost finished w/ the foaming of the front of my chest piece. I have some pieces that still need fabrication and some that need modification. As I said, some of the templates are not translating to foam well or even the correct size(!?!?!) Not sure how that happened but This is what I have so far:
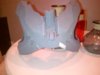
I know......I know.......the center piece is tilting a little to the left, I just couldn't get it to sit straight while holding it till the glue dried. I mighty have to cut out that whole center section and redo. Either the templates were not cut exactly or the foam pieces......or it's just me........I'm also seeing the difference between the pep print-out and the "screen shot".
Pep looks nothing like this
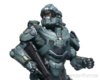
That's all for now folks, see you after the weekend. Now is time for some fun and sun at the beach.......don't forget the drinks!!!!!! (and I wonder why I still have the spare tire!!!!)