- Member DIN
- S011
The weird way mawrTRON uses acrylic paints on foam
Introduction:
This is a comprehensive guide on how to use acrylic paints to paint/weather armour the way I do..
After using rattle cans on my first 2 suits I decided to give acrylic paints a try.
A part from the low cost and low toxicity of acrylics, they also offer a lot of flexibility with tinting colour which I was pretty keen to explore.
Please enjoy this step by step guide loving crafted by myself, mawrTRON.
Much love 405th.
Equipment/Materials
Colour matched acrylic house paint test pots
Acrylic house paint white test pot
Heat gun
PVA glue (2 litres or more)
Plastic cups
Mixing sticks
Variety of paint brushes
Acrylic Craft Paints (Raw Umber, Burnt Sienna, Black, White, Metalic silver)
Rags
Step 0. Temperature/humidity
As with all painting, temperature plays a big part in the drying process. As acrylic paint is waterbased you want to ensure that you are doing this in summer. The paint can absorb moisture from the aid and take days to dry.
The temperatures at the time that this tutorial was made ranged between 25C - 38C (77F - 100F)
Step 0.5 Test Pieces
As there are literally 1000's of different brands of paint and PVA out there I strongly suggest testing this whole method from start to finish on a piece of scrap foam with the products you are planning to use.
Not only does this allow you to see if there will be any reactions with your specific paint/glue, but it also gives you a chance to practice the technique before committing to your whole suit.
YOU HAVE BEEN WARNED!!
Step 1. Colour Matching
I have created a video on how to match from an on screen colour to a physical colour. You can use what ever colour you want but this is my method.
Step 2. Sealing Foam
Once your foam piece is completed, pass over the entire piece with a heat gun to close the cells of the foam. Not too toasty, just enough to make the foam turn slightly glossier.
Firstly you want to create a 'key' layer for the rest of the paint to stick to. With a 50/50 mix PVA glue and water in spray bottle saturate the suit.
Don't worry about the drips! As the water evaporates from PVA it will level itself out. You will how ever need to be on drip duty towards the end of the drying.
You will notice that once the PVA has dried in on most of the surface the lower edges will still have drips forming.
This is time for the Drip Police™ to move in. With clean rag dab the drips away.
**FUN FACT** PVA Dries clear! **FUN FACT**
Once the entire suit is dry, repeat this step again to add another 50/50 coat of PVA.
Once the 2nd 50/50 coat is dry brush on pure PVA onto the piece. To level out the coat while the glue is still wet, dip your brush in water brush lightly over the top. This method is called 'laying off' which is a term that all you painters out there will be familiar with.
Once the suit is dry repeat this step again.
Although this should be enough coats, try painting your colour onto a test piece and see how the paint reacts.
As a reference I added x3 coats before using paint.
Note that 5mm anti fatigue foam typically has larger cells than EVA high impact floor mats and may require additional coats.
Essentially if your entire suit has a semigloss/satin sheen, you are on the right track.
Step 3. Painting
Ensure you have a variety of brush sizes.
As there are an endless number of PVA glues and paints in the world. Conduct a test of the paint on a smaller piece to ensure the paint does not react with the PVA coat (As mention in Step 0.5). If a reaction occurs an acrylic primer may need to be used.
PVA (in undercoat form) is used in the UK as a primer which means you can paint directly on top of it. Apply your primary colour onto the suit first and allow to dry. Aim to apply the paint as evenly as possible.
Paint is designed to even out as it dries which helps this whole process.
If you have the odd streak don't worry, we call this 'Improvised Weathering™'
Apply additional coats if necessary.
With your smaller brushes start to paint the accent pieces and any other details on the suit. Try to not drink too many coffees or Red Bulls for this step as a steady hand is required.
Step 4. First Stage Weathering
In a separate cup, mix a portion of your base colour with a small amount of the white house paint to create a slightly lighter shade. With a dry brush, dab the paint on all leading and high edges of the armor that would be susceptible to wear and tear. Then with a dry rag, dab and remove a portion of the paint. Allow to dry
What you are trying to create is the illusion that the painted metal has been buffer to a lighter colour.
If you look closely at this image you can see a lighter shade of blue on the high areas of the piece.
Step 5. Resealing
Much like in step 2, the paint will be sealed under a coat of PVA.
With the 50/50 mix of PVA and water, respray the suit until you are satisfied with the gloss level.
You will have to be on drip patrol once again.
What this step does is not only remove the flat finish of the paint, but it also creates a slippery layer for the acrylic weathering paints to slide around on.
Typically when weathering on top of an acryllic paint, the acrylic will absorb the weathering too quickly with unsatisfactory results.
Oh and as a bonus, it is adding a protective layer to the paint!
Note that this can make the paint milky looking of the PVA is applied without ample drying time.
Don't worry, I freaked out too. But everything settles down in the end
Step 5. Weathering
Once everything is 100% dry. (Leave it for a day or 2) Mix the black, raw sienna and raw umber craft paints in a cup with water. What you are trying to achieve is a black/brown colour with the consistency milk.
Section by section brush/drip the desired area with the mixture being sure to get into all the nooks and crannies. Then with a push, swirl, rub and dab as much as you trying to remove the paint.
The trick is to add weathering in small increments, thats how it would happen in real life right?
Please note that there here is no real method or trick of doing this, get messy and have some fun.
Step 6. Paint scratches
Typically when finishing the weathering on a halo suit, people will use an old brush with a metallic silver paint to brush all the high edges. This gives the appearance that the armour has been grazed up against things.
However, for the suit I am working on the character has visable darker wear and tear. Which I will attempt to replicate by replacing the silver with a dark grey/silver/black mix
With a dry brush, proceed to brushing the desired areas with the wear.
Pro tip, Don't throw out those old mangy brushes, they make great dry brushes for this part of the process. The more ruined, the better
Bonus Step.
If you are unhappy with the gloss level of the finished piece and want it shinier, grab your 50/50 mix of PVA/Water and give it another coat or two.
As an added benefit this will seal in any weathering you have done. I tested this on one of my knees and it worked just fine!
I hope this tutorial has helped you, looking forward to seeing your fine work.
<3 mawrTRON
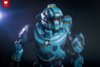
Introduction:
This is a comprehensive guide on how to use acrylic paints to paint/weather armour the way I do..
After using rattle cans on my first 2 suits I decided to give acrylic paints a try.
A part from the low cost and low toxicity of acrylics, they also offer a lot of flexibility with tinting colour which I was pretty keen to explore.
Please enjoy this step by step guide loving crafted by myself, mawrTRON.
Much love 405th.
Equipment/Materials
Colour matched acrylic house paint test pots
Acrylic house paint white test pot
Heat gun
PVA glue (2 litres or more)
Plastic cups
Mixing sticks
Variety of paint brushes
Acrylic Craft Paints (Raw Umber, Burnt Sienna, Black, White, Metalic silver)
Rags
Step 0. Temperature/humidity
As with all painting, temperature plays a big part in the drying process. As acrylic paint is waterbased you want to ensure that you are doing this in summer. The paint can absorb moisture from the aid and take days to dry.
The temperatures at the time that this tutorial was made ranged between 25C - 38C (77F - 100F)
Step 0.5 Test Pieces
As there are literally 1000's of different brands of paint and PVA out there I strongly suggest testing this whole method from start to finish on a piece of scrap foam with the products you are planning to use.
Not only does this allow you to see if there will be any reactions with your specific paint/glue, but it also gives you a chance to practice the technique before committing to your whole suit.
YOU HAVE BEEN WARNED!!
Step 1. Colour Matching
I have created a video on how to match from an on screen colour to a physical colour. You can use what ever colour you want but this is my method.
Step 2. Sealing Foam
Once your foam piece is completed, pass over the entire piece with a heat gun to close the cells of the foam. Not too toasty, just enough to make the foam turn slightly glossier.
Firstly you want to create a 'key' layer for the rest of the paint to stick to. With a 50/50 mix PVA glue and water in spray bottle saturate the suit.
Don't worry about the drips! As the water evaporates from PVA it will level itself out. You will how ever need to be on drip duty towards the end of the drying.
You will notice that once the PVA has dried in on most of the surface the lower edges will still have drips forming.
This is time for the Drip Police™ to move in. With clean rag dab the drips away.
**FUN FACT** PVA Dries clear! **FUN FACT**
Once the entire suit is dry, repeat this step again to add another 50/50 coat of PVA.
Once the 2nd 50/50 coat is dry brush on pure PVA onto the piece. To level out the coat while the glue is still wet, dip your brush in water brush lightly over the top. This method is called 'laying off' which is a term that all you painters out there will be familiar with.
Once the suit is dry repeat this step again.
Although this should be enough coats, try painting your colour onto a test piece and see how the paint reacts.
As a reference I added x3 coats before using paint.
Note that 5mm anti fatigue foam typically has larger cells than EVA high impact floor mats and may require additional coats.
Essentially if your entire suit has a semigloss/satin sheen, you are on the right track.
Step 3. Painting
Ensure you have a variety of brush sizes.
As there are an endless number of PVA glues and paints in the world. Conduct a test of the paint on a smaller piece to ensure the paint does not react with the PVA coat (As mention in Step 0.5). If a reaction occurs an acrylic primer may need to be used.
PVA (in undercoat form) is used in the UK as a primer which means you can paint directly on top of it. Apply your primary colour onto the suit first and allow to dry. Aim to apply the paint as evenly as possible.
Paint is designed to even out as it dries which helps this whole process.
If you have the odd streak don't worry, we call this 'Improvised Weathering™'
Apply additional coats if necessary.
With your smaller brushes start to paint the accent pieces and any other details on the suit. Try to not drink too many coffees or Red Bulls for this step as a steady hand is required.
Step 4. First Stage Weathering
In a separate cup, mix a portion of your base colour with a small amount of the white house paint to create a slightly lighter shade. With a dry brush, dab the paint on all leading and high edges of the armor that would be susceptible to wear and tear. Then with a dry rag, dab and remove a portion of the paint. Allow to dry
What you are trying to create is the illusion that the painted metal has been buffer to a lighter colour.
If you look closely at this image you can see a lighter shade of blue on the high areas of the piece.
Step 5. Resealing
Much like in step 2, the paint will be sealed under a coat of PVA.
With the 50/50 mix of PVA and water, respray the suit until you are satisfied with the gloss level.
You will have to be on drip patrol once again.
What this step does is not only remove the flat finish of the paint, but it also creates a slippery layer for the acrylic weathering paints to slide around on.
Typically when weathering on top of an acryllic paint, the acrylic will absorb the weathering too quickly with unsatisfactory results.
Oh and as a bonus, it is adding a protective layer to the paint!
Note that this can make the paint milky looking of the PVA is applied without ample drying time.
Don't worry, I freaked out too. But everything settles down in the end
Step 5. Weathering
Once everything is 100% dry. (Leave it for a day or 2) Mix the black, raw sienna and raw umber craft paints in a cup with water. What you are trying to achieve is a black/brown colour with the consistency milk.
Section by section brush/drip the desired area with the mixture being sure to get into all the nooks and crannies. Then with a push, swirl, rub and dab as much as you trying to remove the paint.
The trick is to add weathering in small increments, thats how it would happen in real life right?
Please note that there here is no real method or trick of doing this, get messy and have some fun.
Step 6. Paint scratches
Typically when finishing the weathering on a halo suit, people will use an old brush with a metallic silver paint to brush all the high edges. This gives the appearance that the armour has been grazed up against things.
However, for the suit I am working on the character has visable darker wear and tear. Which I will attempt to replicate by replacing the silver with a dark grey/silver/black mix
With a dry brush, proceed to brushing the desired areas with the wear.
Pro tip, Don't throw out those old mangy brushes, they make great dry brushes for this part of the process. The more ruined, the better
Bonus Step.
If you are unhappy with the gloss level of the finished piece and want it shinier, grab your 50/50 mix of PVA/Water and give it another coat or two.
As an added benefit this will seal in any weathering you have done. I tested this on one of my knees and it worked just fine!
I hope this tutorial has helped you, looking forward to seeing your fine work.
<3 mawrTRON
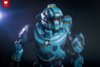
Last edited: