Hi, everyone. I just recently started my first full, 3D printed armor build! Naturally, my first and only choice was to do Master Chief.
I'm using the Halo Infinite design from Galactic Armory for the armor, and I found some files on Etsy for the under-suit. It might be more trouble than its worth, but I'm attempting to print all the joint details in soft TPU. The ankle pieces that I've printed seem to be working great so far...
Current problem I'm dealing with, is sizing the chest and back pieces. Apparently, my rib cage is wider than "normal". Lol. I don't wanna just scale up the chest piece, as this will restrict my shoulder and arm movements... I was thinking of using a heat gun to widen the connections around my rib cage. Does anyone have any better ideas that have worked for them in the past for "stretching" parts without just scaling up the whole part??
For the boots, I sliced off the bottom half inch, printed that separately, and will be attempting to cast a mold with a hard urethane rubber.
Also, any tips/tricks you have to help me avoid those rookie mistakes would be greatly appreciated!
I'll try to keep updated with new pics as I progress with my build. Thanks! (My cat's name is Moby, and he still doesn't know what to make of the armor...
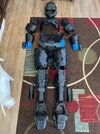
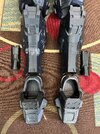
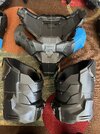
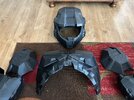
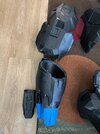
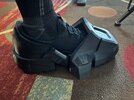
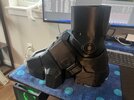
)
I'm using the Halo Infinite design from Galactic Armory for the armor, and I found some files on Etsy for the under-suit. It might be more trouble than its worth, but I'm attempting to print all the joint details in soft TPU. The ankle pieces that I've printed seem to be working great so far...
Current problem I'm dealing with, is sizing the chest and back pieces. Apparently, my rib cage is wider than "normal". Lol. I don't wanna just scale up the chest piece, as this will restrict my shoulder and arm movements... I was thinking of using a heat gun to widen the connections around my rib cage. Does anyone have any better ideas that have worked for them in the past for "stretching" parts without just scaling up the whole part??
For the boots, I sliced off the bottom half inch, printed that separately, and will be attempting to cast a mold with a hard urethane rubber.
Also, any tips/tricks you have to help me avoid those rookie mistakes would be greatly appreciated!
I'll try to keep updated with new pics as I progress with my build. Thanks! (My cat's name is Moby, and he still doesn't know what to make of the armor...
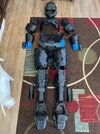
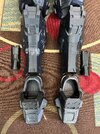
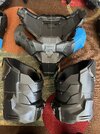
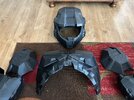
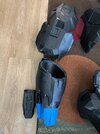
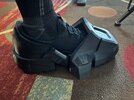
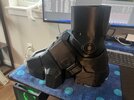
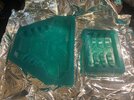