Okay. Got some more updates! Over this week, we've had some ups and some downs. But we'll start with the good news right now.
The scope tube components have been printed and will need to be polished up. But now I can work on fitting the scope components into the printed parts. So with the scope, I have the two halves of the tube printed, the 7x retainer, and the mount for the camera all printed.
I also re-printed the camera mount since the first time it came out really rough.
And I started putting some of the components in place in the tube.
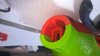
I also started working on making the steel components at a machine shop on Friday.
I started by cutting out the pieces for the hammer pieces.
And then marked the centers for the dowel pin holes to be drilled.
The holes were then drilled and reamed for a 1/8'th inch rod to fit in.
And the skids were also started. 2inch wide by 1/5 inch high steel plate was cut in 1.5 inch wide pieces to form the base shapes of the skids for the bipods.
A hole was then drilled through for a 5/16th screw and a counter bore was then added so the bolt would be recessed.
These steel blocks will then be taken to a mill so I can machine out the slot in the center. The hammer parts are being micro-welded right now.
Ok. so that's where I'm at with parts. I still need to finish the surfaces of the muzzle break and the scope tube.
Now for the bad. On Thursday morning I spoke with our CNC shop manager about making a couple of parts in the shop, specifically the magazine shells. He said that our machines could make the two pieces, so I went out and purchased a $150 chunk of aluminum for the mag shells. About a half hour after I made the order, I received an email from my professor forwarding me an email from the shop manager to my professor and CC'ing the Dean of engineering asking if the project would be acceptable. Apparently the shop manager did a quick google search and saw one website that said airsoft was illegal in Chicago, which is incorrect. My professor asked if we could revise the project and I agreed (which I'll explain what we will be doing in a bit). After speaking with my friend who is a Chicago police officer confirming that you can own airsoft guns in Chicago, but just not bring them out in public, as well as looking up the specific Chicago ordinance stating that airsoft components can be manufactured in Chicago so long as the parts will be transported intrastate, interstate, or overseas (which is the intent), I spoke with my professor again. He agreed with me that there was a misunderstanding of the project and of Chicago laws. He also reached out to the shop manager some (my professor is totally for this project and thinks this issue is really stupid which now makes him the coolest college professor at IIT

). So as of right now, we have agreed to not manufacture the part that holds the hop up unit this semester (which is something that I can do on my own to finish this project yay!). We are trying to tip-toe around the bs bureaucracy of the current situation. As of now we will be able to move forward with the project again. This all made for an interesting 24 hours so we'll see where this goes from here.
This week I am also working on setting up a meeting with some engineers to discuss the manufacturability of components to make things easier to machine. My spring break is also coming soon so I will be able to make some more parts in the coming weeks.