This is my first time working with modeling foam/clay (don't know if there's a difference, the tub says foam...) and I'm very happy with the results. What follows are the steps I've come up with to get to where I am.
First, get some modeling foam/ foam clay
Kneed a small amount in you hand, about 1-2 tablespoons worth, and apply to low poly/ problem spots on the print. The small gaps between the layers seem to help the foam adhere.
Thin the first layer as much a possible. I seem to be able to get roughly .4mm thickness before the foam is too thin and starts to tear. Smooth as much as possible
After 12-24 (might vary by foam brand) the first layer should be dry enough to add a second layer. For this I take a similar amount of foam and stick some down, stretch it some before pressing the clump down again, do this in a line or zig-zag to better cover the area. Wet the new layer until slick and with wet fingers spread and smooth as needed.
After another 24-48 hours it's dry enough to sand. The above steps can be repeated as needed if hard edges are visible before sanding.
I sanded with 320 grit until mostly smooth, making sure to flatten the edges of the foam as flush to the print as possible. Again, the above steps can be repeated if needed. Be sure to let everything dry well before sanding or you might tear or rip the foam off the print.
If you haven't put your PPE on yet its definitely time to as we are breaking out the bondo spot putty. Apply as needed to smooth dents in the foam and mesh the edges to the print for a seamless look.
After the bondo is dry sand as needed/desired, add bondo or filler primer depending on initial results/personal preference/skill and continue to prep for paint/finishing.
Before foam
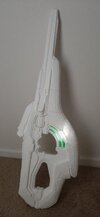
Sharp angles under the barrel, on the stock and cheek rest.
After 2 foam layers
I did add more after this photo was taken. You could still see some of the edges.
First unsanded bondo layer on some of the prop
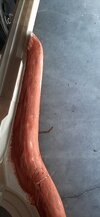
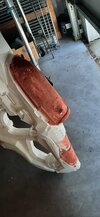
This will smooth out with sanding. Haven't gotten that far yet XD
If this is new information for some I hope it helps! I'm glad that I don't need to reprint bits of armor or break my hand sanding edges now!