Well done on the AR, it looks glorious. And that carbine...epic. Can't wait to see more.
Wow these weapons are beautiful!
Thanks guys! glad people are enjoying my builds.
Now then, after another little hiatus thanks to other projects taking over the 3D printer, the printer breaking down, and other life things, i'm BACK! i've got a nice juicy backlog of props that i've been working on too, so get ready for a BUTTLOAD of pic-heavy posts!
First up, with the carbine done, i was pretty inspired by
Saber's FANTASTIC halo 2 Brute build, so i figured the Brute Spiker would be a good choice for the next prop!
Start off with some printing, as usual:
Started off with the "body" of the spiker, since the blades were seperated to make assembly, detailing, and painting easier down the line. with a good chunk of the main body done, the blades were next:
And, once again, the pants-wetting scale of coenant weapons comes across. these blades are H U G E ! certainly nothing you'd wanna get shanked with by an 800 pound alien gorilla...
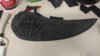
Human hand for scale...
With both blades done, it'd back to printing the body sections!
Now, of course things were going a bit too well, and like i said at the top of the post my printer was having a lot of issues. i debated pretty heavily on including this little breakaway from the build itself, but this issue was so confusing and difficult to diagnose that i feel like it'd be a huge help if anyone found themselves in a similar situation.
So, obviously, the printer broke down. extruder jam. fantastic. However, i disassembled the extruder, cleaned it out, torched it, gave it an acetone bath, basically the 3D printer version of a "Spa day". thinking the problem was fixed, i slapped it back into the toolhead and got printing! ...another jam. however, this time, when i took the extruder out, i found this:
Now, for those of you that didn't immediately go "um what", this is REALLY WEIRD! normally, when your extruder clogs, the toothy gear that feeds the filament into the top of the extruder just gnaws the filament down since, well, it can't go anywhere. you just have to snip off the gnawed up piece of filament and feed it through again. What it DOESN'T DO... is keep pushing the filament down until its compressed into this weird corkscrew shape on top of the extruder's heat sink.
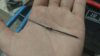
Needless to say, i was flummoxed, and so was the Robo3D technician i called (and have on speed dial at this point). I'll skip the week or two of head scratching and frustration and get to the answer:
As it turns out, there's a fan on the side of the toolhead that helps control the temperature of the extruder. it's basically the coolant for the heat sink that you see pictured above. Now, with the way my workbench is laid out, I can't see this fan when i'm working on my printer. here's the little guy i'm talking about:
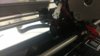
As it turns out, this fan had been sucking up all sorts of crap in the year i've had my printer, and enough hair/thread/gunk had got caught up in the motor to start choking it out. i FINALLY noticed it by complete accident while warming up the printer for another round of maintenance. i could see it spinning up, dying, spooling down, then trying to spin up again over and over. Turns out, when this fan doesn't run properly, the heat sink gets too hot, which means the filament starts melting and getting less solid higher up in the tube, which means it bends/sticks to the tube/gets sticky before its meant to, which means it has enough bend to it to make a corkscrew pattern on top of the heat sink. needless to say, i was ECSTATIC to have finally figured out the problem, and quickly swapped the fan out for a new one i had laying around. so, hopefully this helps some very frustrated people like me.
Unfortunately that's it for this post, next up, more printing! stay tuned!